Ein unbemannter Gabelstapler kommt aus 100 Metern Entfernung auf den Betrachter zugerast, stoppt urplötzlich auf halbem Weg, um sich auf eine Höhe von gut 30 Metern emporzurecken. Er greift eine von 36.000 Paletten, die sich in den Regalen auftürmen, und befördert sie in die Tiefe. Nur der Verwaltungsrechner weiß, welche Schrauben dort oben lagen, wo das rasante Flurförderfahrzeug soeben zugegriffen hat.
36.000 Paletten mit Schrauben
Beim Schrauben-Großhändler Reyher in Hamburg-Altona laufen die meisten Prozesse vollautomatisch ab: Rote Kisten mit neuer Ware wandern auf Fließbändern ins Lager. In grauen Kisten fahren Schrauben vorbei, die die Hallen verlassen. „Ware zum Mann“ nennt sich das Prinzip, nach dem hier gearbeitet wird.
Die Logistiker gehen also nicht mehr ins Lager hinein, sondern die Ware kommt vollautomatisch zu ihnen. „Durchschnittlich dauert es zwei bis vier Stunden vom Auftragseingang an, bis die Ware in den Ausgang geht“, berichtet Jan Reise, Key Account Manager bei Reyher, der im Unternehmen Kunden aus der Windbranche betreut.
Zeit ist Geld, auch in der Windkraftlogistik. „Just in time“ heißt bei Reyher: Der Kunde sagt, wann er die Ware haben will. Oft bestellt er heute und bekommt schon morgen seine Lieferung. So oder so sind die Schrauben meist pünktlich auf der Baustelle. Mit dem Hausspediteur Bursped, Mitglied des Cargoline-Verbunds, verlassen pro Tag rund 250 Tonnen Verbindungselemente den Logistik-standort in Hamburg. Von den dahinter stehenden circa 3.200 Kundenaufträgen täglich entfallen etwa zehn Prozent auf die Windkraft. Geschwindigkeit und Effizienz lassen sich nicht nur durch Automation im Lager erreichen.
Die Maßnahmen sind wesentlich weitreichender. „Während einige Unternehmen die einzelnen Schraubenpakete auf die Baustelle schicken, liefern wir komplett konfektionierte Bausätze – von der Schraube bis zum Zusatzmaterial wie Besen oder Handschuhe“, erklärt Reise. Auf der Baustelle greifen sich die Monteure die nach Bereichen in der Turbine farblich sortierten Sets. Dadurch spart der Kunde Zeit und Geld. Bei Reyher stehen dafür die entsprechenden Kartons bereit, auf denen der Name des Kunden und die Montageeinheit zu lesen ist, etwa die Nabe. Darin befinden sich wiederum kleine, ebenfalls beschriftete Kartons für die einzelnen Bereiche an dem Bauteil.
Steckt der Lkw fest, wird es teuer
Reyher ist nicht das einzige Unternehmen, das auf die Bedürfnisse der Kunden mit zusätzlichen Servicedienstleistungen wie dem bedarfsgerechten Vorpacken von Sets eingeht. Zarges stattet Windkrafttürme mit allen Turminnenausbauten wie Service-Liften, Leitern, Plattformen, Elektropaketen und so weiter aus. „Bis zu 3.000 Bauteile sind das“, sagt Arnold Wagner, Vertriebsleiter der Zarges-Division Wind, Tochterfirma Niord. Turmbauer erhalten dann ohne weitere Aufwendungen die kompletten Einbauten als Kitset – montagefertig und just in time. Auch hier geht es wieder darum, dass der Kunde die kleinen und großen Zulieferteile zügig verbauen kann. Zeitersparnis gehört heute zu den ausschlaggebenden Verkaufsargumenten.
Warum ist die Lieferung just in time überhaupt so wichtig? Enercon-Logistikchef Mathias Moser erklärt: „Weil auf der Baustelle Kran und Team stehen, die 20.000 oder 30.000 Euro am Tag kosten. Und wenn ein Rotorblatt zu spät geliefert wird, kann niemand weiterarbeiten.“ Projektlogistik sei das am wenigsten planbare Glied der Kette. „Da kann man noch so lange Vorlaufzeit haben: Wenn die Polizei nicht kommen kann, um den Transport zu begleiten, weil sie zu einem anderen Einsatz muss, dann habe ich Verzögerungen, die viel Geld kosten. Und die kommen nicht selten vor“, so Moser.
Zehn bis 15 Prozent der gesamten Projektkosten eines Onshore-Windparks entfallen auf die Logistik. Offshore sind es sogar 20 bis 25 Prozent. Im Automobilsektor sind es fünf Prozent. Zug- und Flugzeugbau, die sich aufgrund der Größe der Bauteile besser mit der Windkraft vergleichen lassen, kommen auf zehn Prozent. Das heißt, in der Windkraft lassen sich die Logistikkosten möglicherweise noch leicht reduzieren. Zulieferer und Hersteller sind aufgrund eines angespannten Marktumfelds branchenweit mehr denn je zum Sparen angehalten. Doch das Thema ist komplex: Spart man auf der einen Seite, wird es oftmals auf der anderen teurer. Ein kurzer Transportweg führt zu einem weniger preiswerten Lieferanten. Ein günstiger Zulieferer kann die Zeitpläne nicht einhalten. Zudem muss sich die Windindustrie als Lieferantin sauberer Technologie die Frage gefallen lassen, wie umweltschonend ihre Logistik ausgestaltet ist.
Auch wenn die Turbinenschmieden inzwischen recht gut aufgestellt sind, was ihre Lager- und Transportkonzepte anbelangt – Optimierungspotenzial gibt es reichlich. Wolfgang Kersten, Leiter des Instituts für Logistik und Unternehmensführung an der Technischen Universität Hamburg-Harburg, hat gemeinsam mit der Unternehmensberatung Putz und Partner wiederholt empirische Studien zum Risikomanagement der Windkraftlogistik durchgeführt und kann daraus Veränderungen im Zeitverlauf ableiten. „Heute sind die Strukturen globaler und gleichzeitig schlanker. Dadurch ist das Risiko gestiegen“, sagt er.
Überdimensionierte Lager kosten unnötig
Bei einem Vergleich mit der Automobilbranche kommt er zu dem Schluss, dass die Logistikstrukturen in der Windenergie noch deutlich weniger ausgereift sind. In der Fahrzeugindustrie werde wesentlich mehr just in time geliefert. „Dort spricht man von einer Verlagerung der Lagerhaltung auf die Straße.“ Extrem schlanke Strukturen sind dort also bis an die Grenzen des Möglichen umgesetzt worden. Ein überdimensioniert ausgelegtes Servicelager mit mehr Ersatzteilen als nötig binde unnötig viel Kapital, sagt Simone Runge.
Die Leiterin der Fachgruppe Supply Chain Design am Forschungsinstitut für Rationalisierung an der RWTH Aachen beschäftigt sich mit dem Ersatzteilnetzwerk. „Die grundlegende Fragestellung bei der Anpassung der Logistikstrukturen ist immer, ob eine Zentralisierungsstrategie, die geringere Kapitalbindung bedeutet, oder eine dezentrale Struktur mit entsprechender Markt- und Kundennähe zu bevorzugen ist“, fasst Runge zusammen. Sie liefert ein theoretisches Denkspiel: „Könnte man alle Instandhaltungen 100-prozentig vorhersehen, so könnte die Anlieferung der Ersatzteile aus einem Zentrallager genau zur richtigen Zeit erfolgen.“ So ließe sich die Anzahl an Ersatzteilen im Lager reduzieren. „In der Realität steht diesem Modell das Risiko gegenüber, dass die Anlagen über längere Zeit stehen, weil doch etwas Unvorhergesehenes geschehen ist.“
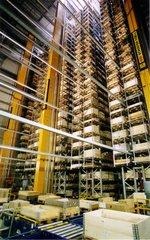
Sebastian Peiler beschäftigt sich als Leiter Business Development Industrial amp; Electronics des Logistikkonzerns DB Schenker mit Netzwerken und Lagerstrukturen. Das Unternehmen lagert und liefert unter anderem Ersatzteile für Firmen wie Vestas, Enertrag und Repower. „Die schnellste Lieferzeit beträgt zwei Stunden von unseren dezentralen Depots bis zur Anlage, nachdem der Servicetechniker einen Auftrag ausgelöst hat“, sagt Peiler. Das Unternehmen verantwortet ein Zentrallager, drei Regionallager und bis zu 80 Kleinlager in Europa. Hat der Windmüller mit seinem Servicedienstleister einen Vollwartungsvertrag abgeschlossen, garantiert der Service eine technische Verfügbarkeit von üblicherweise 95 bis 98 Prozent. Damit diese eingehalten wird, müssen auch Zulieferer und Logistiker ihre Hausaufgaben machen.
Von dezentralen Strukturen, die sich im Service bewährt haben, verabschieden sich derzeit einige Hersteller, wenn es um Produktionsstandorte geht. „Statt in zahlreichen Ländern Produktionsstätten zu betreiben, fragen sich die Hersteller: ‚Wie können wir die Produktion bündeln?‘“, erklärt Peiler. „Wenn Türme aus Vietnam nach Schweden geliefert werden, schlagen zwei Herzen in meiner Brust: Zum einen ist es eine tolle Transportherausforderung, aber zum anderen eine komplexe Logistikkette.“
Vestas-Europa-Chef Thomas Richterich erklärt dazu, Vestas lasse Türme in der Regel bestimmungsnah fertigen. Auch Vensys-Vorstand Jürgen Rinck erklärt, Türme für Europa kämen keinesfalls vom Hauptgesellschafter Goldwind aus China. „Wir versuchen, die Türme lokal einzukaufen.“ Für ihn ist die Frage interessanter, wie die Türme mit ihren wachsenden Durchmessern noch auf die Baustelle gelangen. Gittermasten oder Holztürme seien da eine gute Lösung.
Gleichwohl, das Thema Billigimporte gibt es bei Türmen längst. In den USA haben heimische Turmhersteller sogar die Einführung von Strafzöllen auf chinesische Türme angeregt. Vestas-Mann Richterich gibt in dem Zusammenhang zu bedenken, dass der Lohn bei Türmen 35 bis 40 Prozent der Gesamtkosten ausmacht. Kommt noch die teure Verschiffung hinzu. Oder ist die etwa erschwinglich?
Reeder fahren meist mit Verlusten
Die Schifffahrt stecke seit Jahren in der Krise, sagt Matthias Mroß, Geschäftsführer der Firma German Renewables Ship Brokers. „Heute fahren sie zwar nicht umsonst, aber zu extrem niedrigen Preisen, weil die Nachfrage des Weltmarkts weit unter dem Angebot an Schiffen liegt.“ Der Reeder fahre im besten Fall zu plus/minus null, meistens jedoch mit Verlusten. Und wenn es zu viel werde, habe der Reeder nur noch drei Möglichkeiten: das Schiff einzumotten und zu warten, bis der Markt besser wird, es zu verkaufen oder es in den Hochofen zu schieben.
Schiffstransporte sind also günstig wie nie. Entsprechend könnte die Rechnung aufgehen, wenn die Windbranche statt teure Produktionsstätten zu betreiben lieber in Billiglohnländern fertigt und die Ware dann zur Baustelle auf der anderen Seite der Erde schippert. Tatsache ist, dass Schiffstransporte in der Windkraft in den vergangenen Jahren zugelegt haben. Ökologisch und sozial ist das allerdings nicht. Vielleicht werden steigende Ölpreise dieser Entwicklung langfristig einen Dämpfer verpassen.
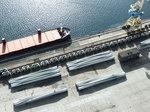
Freilich: Umweltfreundlich ist Logistik ohnehin selten. Das ist in der Windbranche nicht anders als in anderen Wirtschaftsbereichen. Auch hier wird der überwiegende Teil der Aufträge mit dem Lkw als billigstem Transportmittel abgewickelt. „Die Bahn fährt nicht direkt in den Windpark hinein. Das Anliefern und Umladen würde zu lange dauern“, gibt Enercon-Logistiker Moser zu bedenken. 95 Prozent der Bahnstrecken schieden zudem für Transporte von Windturbinenkomponenten von vornherein aus, weil sie elektrifiziert seien. Mit den großen Bauteilen könne man diese Strecken nicht befahren, weil Strommasten und Leitungen weggerissen würden.
„Wir haben das Glück, dass die Strecke zwischen Aurich und Emden nicht elektrifiziert ist“, erklärt Mathias Moser. Enercon hatte zusammen mit der Eisenbahninfrastrukturgesellschaft Aurich-Emden (EAE) die verfallene Bahnstrecke reaktiviert und betreibt auf dieser nun schon seit mehr als fünf Jahren Güterverkehr von den eigenen Produktionsstätten in Aurich und Georgsheil zum Exporthafen Emden. Vier bis fünf Züge fahren dort täglich. Inzwischen erfolgt auch der Zwischenwerksverkehr zwischen den Enercon-Produktionsstätten in Ostfriesland und Magdeburg weitestgehend mit der Bahn. Der Hersteller beschäftigt 18 Lokomotivführer und hat Zulieferer und benachbarte Industrieunternehmen motiviert, ebenfalls auf die Schiene zu gehen.
Schiene orientiert sich an der Straße
„Wir haben dann versucht, das so zu rechnen, dass die Schiene nicht teurer sein darf als ein Lkw. Pro Schieneneinsatz wird entsprechend dem abgerechnet, was wir für den Lkw-Transport zahlen müssten“, erklärt Enercon-Geschäftsführer Hans-Dieter Kettwig. Das Schienen-Modell wurde auf Strecken in ganz Deutschland ausgeweitet, um es effizient auszugestalten. Enercon betreibt in Magdeburg, Lippstadt, Emden, Aurich und Hamm am öffentlichen Schienennetz Logistikzentren, wo von den verschiedenen Lieferanten an dem jeweils für sie günstigsten Knotenpunkt Komponenten zusammengefasst werden. Die werden an den Bahnhof geliefert und Enercon belädt die Züge so, dass sie praktisch ohne Unterbrechung bis zur jeweiligen Produktionsstätte fahren können.
Das funktioniert quasi wie ein Shuttle-Taxi, der Zug kann alle einsammeln. „Die Schiene geht in Magdeburg direkt ans Werk, die Ware direkt aufs Förderband“, berichtet der Enercon-Chef. Lkw würden dort nur Schlange stehen. „All diese Maßnahmen führen dazu, dass die Schiene noch nicht 100-prozentig schwarze Zahlen, aber gute Zahlen schreibt“, resümiert er. Einfallsreichtum gehört dazu, wenn man ungewöhnliche Wege beschreitet. Enercon-Gesamtproduktionsleiter Klaus Peters nutzt die ungeteile Aufmerksamkeit des Publikums bei seinem Vortrag auf der Hannover Messe, um Werbung für die Bahn zu machen. Er spricht Jan Reise direkt an: „Reyher haben wir bis jetzt noch nicht überzeugen können.“ Aber vielleicht ja bald. Enercon bleibt jedenfalls beharrlich. (Nicole Weinhold )
Dieser Beitrag erschien erstmals in der Mai-Ausgabe 2013 von ERNEUERBARE ENERGIEN - Das Magazin.