Die Ludwig-Sütterlin-Straße gehört zu einem kleinen, neu erschlossenen Gewerbegebiet am Stadtrand von Bremen. Zwei Bürohäuser mit drei Etagen sind der Stolz dieser Straße. Entlang des 200 Meter langen Asphaltstreifens mit beinah direkter Anbindung an die Autobahn 27 gibt es sonst nur viele freie Parkplätze und ungenutztes Bauland. Hier teilt sich Emilio Reales die Büroflächen mit seinen neun Ingenieuren, einem Architekturbüro und anderen Dienstleistern. Wenn alles läuft wie geplant, wird sein Unternehmen Maritime Offshore Group (MOG) von hier aus die Welt der Offshore-Fundamente revolutionieren. Mit dem Hexabase-Fundament, einer aufgelösten Jacket-Struktur, die, anders als bisherige Fundamenttypen, komplett aus standardisierten Rohren besteht.
Dass gerade erst der Fundamentbauer Weserwind im benachbarten Bremerhaven seine Mitarbeiter in die Kurzarbeit geschickt hat, irritiert Emilio Reales nicht. Auch wenn er das bedauert, sieht Reales sein eigenes Konzept im Straucheln von Weserwind bestätigt. „Viele Fundamenthersteller sind reine Schweißbetriebe ohne eigenes Design. Ihnen fehlt das Alleinstellungsmerkmal“, sagt Reales. Dabei ist Weserwind bislang der Fertigungsspezialist für Tripod-Fundamente der Areva-Turbinen und für Jacket-Gründungen der Senvion-Anlagen gewesen. Dennoch klafft jetzt eine Auftragslücke. Die letzten Tripods sind ausgeliefert. Bliebe noch der Ostsee-Windpark Baltic II, wo 41 Jackets installiert werden. Projektentwickler EnBW hat sich aber für einen anderen Lieferanten entschieden: Bladt fertigt die Jackets in Dänemark.
Leben mit dem Kostendruck
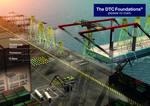
Der Kostendruck lastet auf der Offshore-Branche. Gleichzeitig kämpft sie mit politischer Unsicherheit und muss zumindest nationale Auftragsflauten überbrücken können. Die Fundamenthersteller verfolgen verschiedene Konzepte, um die Produktionskosten auch in diesem innovationsfeindlichen Umfeld nachhaltig zu senken.
Für die Maritime Offshore Group ist der Preiskampf nur ein Preiskampf der Konzepte und keiner zwischen den Lieferanten. Denn es gibt nur einen Anbieter des Hexabase: Wer sich für das Fundament entscheidet, kauft exklusiv beim Kooperationspartner Thyssen-Krupp Mannex (TKM), einer Tochter der Thyssen-Krupp AG. Die Patentrechte der MOG sichern den Unique Selling Point: Das Hexabase verspricht konzeptbedingt eine Kostenersparnis von 20 bis 30 Prozent gegenüber einem herkömmlichen Jacket-Fundament bei 40 Meter Wassertiefe.
Hinzu kommt laut MOG eine größere Sicherheit für den Kunden. Lieferkette, Herstellung und Vertrieb laufen über TKM. Und damit auch die Gewährleistung. „Die Fundamentkosten eines einzigen Windparks mit Hexabase liegen bei rund einer viertel Milliarde Euro. Der Kunde benötigt finanzielle Sicherheit, das kann ein mittelständisches Unternehmen nicht in dieser Höhe stemmen. Im Falle einer Gewährleistung wäre es ruiniert“, sagt Reales.
Für Ende März (nach Redaktionsschluss dieser Ausgabe) erwartet MOG die Zertifizierung nach DNV GL. Direkt im Anschluss erfolgt die Zertifizierung eines neuen Korrosionsschutzkonzepts. Ein Prototyp in der deutschen Nordsee soll dieses Jahr folgen. Diesen Schritt geht Emilio Reales aber eher zähneknirschend, denn er kostet zusätzlich Zeit und Geld: „Vom Airbus hat man auch kein Testmodell gebaut, um zu sehen, ob der auch wirklich fliegt. Den baut man und fliegt los.“
Optimieren in kleinen Schritten
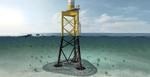
Doch die Offshore-Branche ist von Natur aus vorsichtig und das Hexabase muss für verbindliche Bestellungen um Vertrauen werben. 80 Fundamente wären nötig, um eine Fertigungsstraße aufzubauen und für ein Jahr auszulasten. Dann würden auch Kostensenkungseffekte schon voll greifen. Beim Hexabase entfallen komplizierte Sonderbauteile, die aufwändig handgeschweißt werden müssen, komplett. Dazu zählen beispielsweise die konischen Stahlelemente, wie sie bei Jacket und Tripod heute verschweißt werden.
Die abwartende Haltung der Offshore-Industrie, die Emilio Reales plagt, hält Peter Schaumann, der Leiter des Instituts für Stahlbau an der Universität Hannover, prinzipiell für eine nachvollziehbare Einstellung: „Wir gehen in kleinen Innovationsschritten voran. Ich halte das für den richtigen Ansatz.“ Damit bezieht sich Schaumann auf die Lehren, die die Offshore-Industrie mit ihren Fundamenten schon ziehen musste. Sie sucht nach Lösungen für die bestehenden Schwächen aktueller Konzepte. Und diese Arbeit folgt weniger dem Grundsatz günstiger Fundamentdesigns. Denn: „Nach wie vor gilt als eine der größten Offshore-Lehren: Das Geld wird bei der Installation auf See verdient oder verbrannt“, sagt Schaumann.
Eine andauernde Schwäche von Monopile, Jacket und Tripod liegt laut Schaumann in der Stahl-Mörtel-Verbindung, den sogenannten Grout-Verbindungen. Der Mörtel wird unter Wasser zwischen Turm und Gründung gepumpt, eine Dichtung hindert ihn am Auslaufen – meistens. „Bei der Ausführung gibt es häufiger
Probleme, zum Beispiel weil die Dichtung nicht richtig funktioniert“, sagt Schaumann. Die Korrektur solcher Fehler im Baufeld kostet viel Zeit und Geld. „Was man durch optimiertes Design eingespart hat, geht damit verloren“, sagt Schaumann.
Einen Lösungsansatz dafür testet Energieversorger Eon aktuell im Offshore-Windpark Amrumbank West. Hier sollen Monopiles und Türme nicht mehr vergroutet, sondern mit 72 Millimeter starken Schrauben verschraubt werden. Eine weitere Variante, um die Installation auf See zu vereinfachen, verspricht das sogenannte Bucketfundament. Das Konzept dieser Gründung beruht auf einem Stahlzylinder, der an der unteren Seite offen ist; damit ähnelt er einem auf den Kopf gestellten Eimer. Saugpumpen am Stahlzylinder erzeugen einen Unterdruck, wodurch er sich in den Meeresboden gräbt. Die Universität Hannover untersucht dieses Gründungskonzept seit Juni 2012 zusammen mit dem Fraunhofer Windinstitut IWES im Projekt Windbucket.
Laut Schaumann schlägt man mit diesem Fundament gleich drei Fliegen mit einer Klappe: „Das Vergrouten unter Wasser entfällt, wir erzeugen bei der Installation keinen Rammschall und können noch einmal nachjustieren, falls sich herausstellt, dass die Konstruktion nicht so gerade ist, wie sie sein soll.“ Außerdem lässt sich das Fundament problemlos wieder aus dem Meer entfernen.
Die potenziellen Vorteile des Bucketfundaments hat auch der weltgrößte Offshorewind-Projektierer Dong Energy erkannt. Dong will dieses Jahr eine neue Variante des Suction Bucket im Windpark Borkum Riffgrund in der deutschen Nordsee testen. Ein Glücksfall für SPT Offshore, den niederländischen Entwickler des Konzepts. Denn häufig scheitern neue Konzepte schlicht an der vergeblichen Suche nach einem Investor, der den Prototyp finanziert.
Anlagen auf Eimern
Die neue Konstruktion besteht aus drei Buckets als Basis für ein dreibeiniges Jacket. Es soll in Wassertiefen zwischen 30 und 60 Meter genutzt werden und sich schneller installieren lassen als heutige Gründungen. Verlaufen die Tests erfolgreich, könne die Bucket-Jacket-Gründung ab 2017 kommerziell eingesetzt werden. Gleichzeitig erlebt aktuell eine Technologie einen Aufschwung, die für große Wassertiefen eigentlich schon totgesagt war: der Monopile. Unternehmen wie Repower haben längst untersucht, ob sich die Einpfahl-Variante auch für Sechs-Megawatt-Anlagen und große Wassertiefen eignet. Mit positivem Ergebnis.
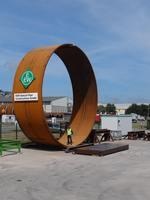
Jetzt rüstet sich der Stahlrohrhersteller EEW Special Pipe Constructions (EEW SPC) für diese Größen. In Rostock baut EEW SPC bis Ende des Jahres eine neue Produktionslinie für Monopiles mit bis zu zehn Meter Durchmesser auf. Wassertiefen von 40 Meter, die bislang Jackets und Tripods vorbehalten waren, sollen damit Monopile-Terrain werden. „Wir gehen davon aus, dass wir in diesen Tiefen gegenüber dem Jacket erheblich günstiger sind“, sagt Michael Hof, Vertriebsleiter bei EEW SPC. Ein Drittel geringere Kosten sind dabei nicht ausgeschlossen.
Die aktuelle Fertigungshalle stößt bei solchen Durchmessern an ihre Grenzen. Dabei wurden in Rostock erst 2013 die weltgrößten Monopiles
für die flachere Windparkhälfte von Baltic II gefertigt: 39 Rohre mit 6,5 Meter Durchmesser. Weitere 41 Turbinen stehen in diesem Windapark bald auf Jacket-Fundamenten.
Kalkulierte Risiken
Bis zu 73,5 Meter messen die einzelnen Piles von Baltic II. Für ein weiteres Offshore-Projekt baut EEW SPC aktuell noch größere Pfähle mit 7,6 Meter Durchmesser. Für den Transport ist das kein Problem. Bei Baltic II etwa wurden die Pfähle vorn und hinten zugestöpselt und schwimmend abtransportiert. „Das Schwierige ist die Logistik in der Produktion“, sagt Hof. Die neue Fertigungsstätte für die Piles mit zehn Meter Durchmesser muss ein erhebliches Gewicht tragen können – ein XL-Monopile wiegt immerhin bis zu 1.500 Tonnen. Gleichzeitig muss sie eine präzise und schnelle Fertigung erlauben, denn das Unternehmen will wöchentlich bis zu drei XL-Piles produzieren können. Dabei hilft die nunmehr fünfjährige Produktionserfahrung in der kleineren Halle. „Anfangs konnten wir dort nur 1,5 Piles pro Woche bauen – bei sieben bis acht Prozent Fehlerrate in den Schweißnähten. Aktuell liegen wir bei wöchentlich sechs Piles mit 0,12 Prozent Fehlerrate“, sagt Hof.
Für EEW SPC ist der Ausbau der Fertigung auch mit hohen Risiken verbunden. 120 Millionen Euro hat das Unternehmen in den Standort Rostock investiert. Sicherheit bringt der große internationale Kundenstamm des Unternehmens. „In der Vergangenheit war unser Hauptmarkt England. Heute versuchen wir, die komplette Nord- und Ostsee zu beliefern“, sagt Hof. Dennoch bleibt ein Restrisiko, dass politisch verursachte Flauten im deutschen Offshore-Geschäft eine Kerbe in die Bilanz schlagen. „Ein Monat Leerlauf kann das ganze Jahr verderben. Deswegen ist eine konstante Auslastung der Produktion elementar wichtig“, sagt Hof.
Die Branchenentwicklung spricht für die Investition von EEW. Das bestätigt auch Peter Schaumann von der Universität Hannover: „Die Weiterentwicklung der Monopiles und der Einsatz von Bucketfundamenten anstelle von Rammarbeiten scheinen mir am erfolgversprechendsten.“ Eine Daseinsberechtigung hat laut Schaumann aber jedes Konzept, das die aktuellen Kosten um mindestens zehn Prozent senken kann.
Bei Emilio Reales stapeln sich die Ideen, um die Kosten der Offshore-Strukturen zu senken. Modelle von Hexabase, Pentabase und anderen Fundamenttypen reihen sich im Konferenzraum von MOG am Bremer Stadtrand aneinander, daneben steht der Eigenentwurf eines Installationsschiffs in einem Glaskasten. Emilio Reales versteht MOG auch als Logistikdienstleister: „Nur Systeme überleben. Und wir können diese Systeme anbieten.“ Am Ende eines solchen Systems kann für größtmögliche Effizienz ein passendes Schiff stehen. Am Anfang steht – viel wichtiger – ein schlüssiges Fertigungskonzept.
Mehr Industrie wagen
Das hat MOG detailliert durchgeplant. Das Hexabase-Fundament besteht aus gleichartigen Knoten, Kreuzen und geraden Rohren. Sie alle haben den gleichen Durchmesser und lassen sich teilautomatisiert fertigen. Die Komponenten werden zu einzelnen sogenannten Leitern verschweißt – sechs Leitern bilden ein Hexabase-Fundament. Die einzelnen Bauteile liefern pro Produktionsstandort drei bis vier Zulieferer. Das sind Schweißfachbetriebe, die immer die gleichen Arbeitsschritte machen. „Durch diese Standardisierung bekommen wir eine hohe Qualität und senken die Kosten“, sagt Reales. Diese Strategie hat Reales in seinen Jahren beim Rohrhersteller Mannesmann verinnerlicht, wo er Abteilungen saniert und neue Standorte mit aufgebaut hat: „Je stärker die Aufgliederung, desto effizienter.“
Das Hexabase-Fundament soll sich für alle aktuellen Turbinen eignen. Dazu variieren die Entwickler nur zwei Variablen: Sie passen die Wandstärken der Rohre an und modifizieren die Eigenfrequenz der Konstruktion, indem sie die Abstände zwischen den sechseckigen Ringen des Hexabase-Fundaments verändern. Wassertiefen zwischen 40 und 80 Meter soll das System erschließen. „Das ist die Schmerzgrenze.“ (Denny Gille)
Dieser Artikel ist in der Printausgabe von ERNEUERBARE ENERGIEN von April 2014 erschienen. Hat er ihnen gefallen? Dann holen Sie sich jetzt ein kostenloses Probeabo unseres Magazins.