Die Vielseitigkeit der Einsatzmöglichkeiten der lösbaren „kraft- und formschlüssigen“ Technologie zum Verbinden von rotationssymmetrischen Bauteilen wird bereits durch Anwendungen in nahezu allen Industriebereichen täglich unter Beweis gestellt. Besonders in den Bereichen, in denen die Anforderungen an Technik, Service und Wartung zunehmend steigen, erhöht sich die Akzeptanz zur Nutzung dieser international patentierten Technologie, die bereits im Jahre 2006 mit dem "Innovationspreis Ruhr" ausgezeichnet wurde. Dieser Preis hat mit dazu beigetragen, dass der Bekanntheitsgrad einen enormen Schub erfahren hat. Während die Funktionalität bei der Schaffung von Referenzanwendungen stets im Vordergrund stand, überzeugen nun die nachgewiesenen revolutionierenden Vorteile gegenüber konventionellen Verbindungen, wobei unabhängig vom Durchmesser und der Betriebszeit höchste Belastungen (Druck, Temperatur, Kräfte, Momente) dauerhaft und sicher übertragen werden. An konventionellen Verbindungen führt "eine scheinbare Normalität" zu einem relativ großen Hebelarm, mit dem die zu übertragenden Kräfte auf die Bauteile wirken, da die Schrauben nur außerhalb des Kraftflusses in einem relativ großen Abstand zur lastführenden Anschlusskonstruktion angeordnet werden können. Sowohl die Auflageflächen des Schraubenkopfes beziehungsweise die der Mutter als auch der erforderliche Freiraum zur Platzierung des Schraubenschlüssels oder der Anzugsvorrichtung erfordern diesen insgesamt ungünstigen Abstand. So dass das Wesentliche an der Kraftübertragung zwischen zwei zu verbindenden Bauteilen, ein möglichst direkter Kraftfluß durch die Bauteile, konstruktiv bedingt nicht erreicht werden kann (siehe Bild).
Weitreichende Einsatzmöglichkeiten An nahezu sämtlichen Verbindungsanordnungen, wie sie im Maschinen-, Industrie- und Apparatebau, in der Kraftwerks- und Rohrleitungstechnik sowie bei verfahrenstechnischen und chemischen Anlagen fast ausnahmslos zum Einsatz gelangen, erzeugen die im nachfolgenden Bild dargestellten Belastungen infolge der Stützwirkung der angeschlossenen Zylinderschale gleichgerichtete, sich auf das Dicht- und Tragverhalten einer Verbindung negativ auswirkende Stülpmomente.
Sie erfordern einen entsprechend großen Verformungswiderstand der Bauteile und somit relativ große Bauteilgewichte. Dagegen stellen sich an der vorgestellten Verbindungstechnologie infolge eines optimalen Kraftflusses minimale Stülpverformungen ein. Diese führen zu einer kompakten Bauart, bei der keilförmig ausgebildete Spannelemente zwischen den lösbar zu verbindenden, im Bereich ihrer Stirnflächen metallisch aneinanderliegenden rotationssymmetrischen Bauteilen einen Kraft- und Formschluss erzeugen.
Die Winkel zwischen den Verspannflächen und der Verspannachse sind nicht größer als der Haftreibungswinkel der reibschlüssig zusammenwirkenden Materialien. Sie bewirken eine Selbsthemmung der verspannten Bauteile zueinander, wobei relativ kleine Schrauben, mit denen zuvor der Verspannungszustand erzeugt wurde, einen Übergang von der Haft- zur Gleitreibung - beispielsweise unter dynamischen Belastungen beziehungsweise infolge von Erschütterungen - verhindern. Die Übertragung der (Betriebs-) Belastungen erfolgt nicht über Schrauben, sondern analog dem Wirkprinzip eines Keils über die kraft- und formschlüssig verspannten und zusammenwirkenden Bauteile. Diese anfangs für den Apparatebau entwickelte Verbindungstechnologie ist alternativ an Stelle aller Verbindungen einzusetzen, an denen beispielsweise Schrauben rotationssymmetrische Bauteile verspannen. Unabhängig vom Einsatzbereich, von der zu beachtenden Vorschrift, der konstruktiven Gestaltung, des Durchmessers oder der Betriebstemperatur werden höchste Belastungen sicher übertragen. Bei abdichtenden Verbindungen wie Turmsegmentverbindungen erfolgt die Anordnung einer Dichtung grundsätzlich im Kraftnebenschluß, so dass gegenüber einer im Krafthauptschluß angeordneten Dichtung bedeutend geringere Kräfte zum Vorverformen erforderlich sind. Die vom Dichtungshersteller vorgegebenen Abmessungen der Dichtungsnut begrenzen die auf die Dichtung wirkenden maximalen Kräfte, so dass die für die Dichtheit einer Verbindung erforderlichen Werte in keinem Fall überschritten werden können.
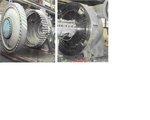
Verbindet Turmsegmente auch mit Fundament
Ebenso werden entsprechend der Betriebstemperatur und der erforderlichen chemischen Beständigkeit in Absprache mit dem Dichtungshersteller die konstruktive Gestaltung der Dichtung (O-/ C-Ring, federverstärkter O-/C-Ring), der Dichtungswerkstoff (Metall / Elastomere), die Toleranzen der Nut sowie die Oberflächengüten festgelegt.
Wirtschaftliche Vorteile ergeben sich somit unter anderem an Verbindungen von zylindrischen Bauteilen untereinander beziehungsweise mit dem Fundament (etwa Windenergieanlagen), zur Vereinfachung und Reduzierung des Transport- und Montageaufwands bei Großanlagen (Offshore-Technik / -Gründungen), zum lösbaren oder dauerhaften Verbinden von nicht oder nur schwer schweißbaren Bauteilen, zur Umgehung von Schweißarbeiten, die anschließendes Induktivglühungen erfordern (Austausch von Verschleißteilen) oder zur konstruktiv einfacheren Gestaltung von Verbindungen, da diese nicht mehr den bisher erforderlichen großen Einbauraum zur Montage von axial angeordneten Schrauben benötigen.
Nicht bekannte oder nicht berücksichtigte Zusatzbelastungen, die als resultierendes Moment auf die Verbindung wirken, können die Dichtheit einer Verbindung nicht mehr beeinflussen. Zudem stehen die auf die Schraubenvorspannung und das Dichtverhalten negativ wirkenden Einflüsse des Kriechens einer im Krafthauptschluß angeordneten Dichtung nicht mehr an.
Spektakuläre Testergebnisse Als Bewertungsmaßstab der gesamten Technologie werden spektakuläre Testergebnisse herausgestellt, die für Anwendungen in allen Industriebereichen neue Maßstäbe setzen. So war bei der BASF AG ein Test geplant, an einer umgestalteten konventionellen 325 bar Rohrleitungsverbindung den Probedruck über die geforderte Druckprobe von 488 bar weiter heraufzusetzen. Bei 1750 bar, mehr als dem 5-fachen des Betriebsdrucks, standen die Rohrkörper mit einer Wandstärke von 25 mm jedoch kurz vor dem Zerbersten. Trotz der relativ großen Wandstärke vergrößerte sich infolge plastischer Verformung der Außendurchmesser der Rohrkörper von 170 auf 215 mm, während die Bauteile der Verbindung keinerlei Beschädigungen zeigten.
Verbindungen von Großwälzlagern
Großwälzlager sind Zwischenbauteile drehbarer oder schwingender Verbindungen. Ihre Aufgabe ist es, große statische und dynamische Kräfte und Momente zu übertragen. Bei den bekannten Verbindungen von Großwälzlagern mit der Anschlußkonstruktion erfolgt die Kraft- und Momentenübertragung ausschließlich durch axial angeordnete und vorgespannte Schrauben aus hochfesten Werkstoffen. Eine ausreichende Dimensionierung und eine sorgfältige Vorspannung bestimmt im wesentlichen die Funktionssicherheit. Die Wartungsvorschriften der Lagerhersteller, insbesondere die Kontrolle der erforderlichen Schraubenvorspannungen sind entsprechend streng.
An der vorgestellten kraft- und formschlüssigen Verbindungstechnologie sind Schrauben an der Übertragung von Betriebsbelastungen nicht beteiligt, demzufolge entfallen die vom Lagerhersteller streng vorgeschriebenen Wartungsvorschriften. Folgeschäden sind somit ausgeschlossen. Zudem wirken sämtliche Kräfte mit dem kleinstmöglichen, überhaupt zu erreichenden Hebelarm auf die zu verspannenden Bauteile. Die auftretenden Stülpmomente in den beiden Lagerhälften sind aufgrund des günstigen Kraftflusses entsprechend gering. Es stellt sich ein optimaler Kraftfluß durch das Lager und durch die Wälzkörper ein, so dass Forderungen nach einer Konzentrierung des Anpressdruckes der Lagerverspannung nahe der Kraftwirkungslinie erfüllt werden. Die Funktionssicherheit der Großwälzlager wird erheblich heraufgesetzt.
Lösung für Monopile-Probleme?
Insbesondere bei Windenergieanlagen aber zeichnet sich auch ein bisher nicht angewandter Einsatz der Technologie als sinnvoll ab:
• zwischen dem Turm von Windenergieanlagen und den Monopile- Grundrohren von Offshore-Anlagen
• zwischen dem Turm einer Windenergieanlage und der Tragstruktur eines Fundamentes von Onshore-Anlagen
Die auch im ERNEUERBARE-ENERGIEN-Bericht "Die Tragfähigkeit ist nicht gegeben vom Juni 2010 beschriebene Problemsituation derzeitiger Monopile-Gründungen bezieht sich auf die in den Meeresboden gerammten zylindrischen Tragrohre mit den daran angeschlossenen vertikal ausgerichteten zylindrischen Tragtürmen von Offshore-Windenergieanlagen. Die zu verbindenden Bauteile sind übereinander gestülpt oder ineinander gesteckt, der Zwischenraum wird mit einem hochfesten Beton - dem sogenannten "vergrouten" - ausgeglichen. An einer Vielzahl von Anlagen wird jedoch infolge der unstetigen Windeinwirkungen der Beton mit Zunahme der Betriebsdauer regelrecht zermürbt mit der Folge, dass die erforderliche Tragfähigkeit nicht mehr gegeben ist.
Weiterentwicklung
In mehreren Windparks weisen die als "grouted joint" bezeichneten Konstruktionen jetzt Rutschungen zwischen den Tragelementen in Größenordnungen von bereits einigen Zentimetern auf. Die mit dem international patentierten kraft- und formschlüssigen Verbindungssystem zu erreichenden Vorteile führen dagegen zu einer wirtschaftlich vorteilhaften sowie dauerhaft sicheren Verbindung. Montagekosten werden ebenso maßgeblich minimiert wie die Lebenszykluskosten.
Das Konstruktionsprinzip oder die kennzeichnenden Merkmale einer bereits zur Patentierung nun angemeldeten Weiterentwicklung basieren vor allem darauf, dass für alle sich ergebenen Montagesituationen an keinem der zusammenwirkenden Bauteile auf der Baustelle Änderungen vorgenommen werden müssen. Verlaufen die Mittenachsen der zu verbindenden Bauteile parallel zueinander, kommt das Konzept zur Ausführung, wobei ein Distanzring gleichzeitig mit dem Bund in axialer Richtung verspannt wird. Der Distanzring weist über den Umfang die gleiche axiale Bauhöhe auf, das axiale Spannmaß ist durch den Distanzring und den Bund gegeben.
Verändert sich gegenüber einer Ausgangssituation der zu verbindenden Bauteile die Winkellage der Mittenachsen zueinander – unter anderem durch Fundamentsetzungen – oder weist ein Monopile nach dem Rammvorgang eine Abweichung zur Vertikalen auf, kommt etwas anderes zur Ausführung. Hier gelangen zwei Distanzringe zur Anwendung, die in axialer Richtung eine über den Umfang stetige Dickenänderung und somit nicht parallel zueinander liegende Stirnflächen aufweisen. Die Ringe sind baugleich, sie können zur Vereinfachung der Montage in Umfangsrichtung mehrteilig ausgeführt werden.
Um Schrägstellungen auszugleichen, ist der anfangs montierte Distanzring lediglich durch zwei Distanzringe mit nicht parallel zueinander liegenden Stirnflächen auszutauschen. Die Entscheidung, welche Dickenänderung die Distanzringe jeweils aufweisen müssen, hängt von der gemessenen Abweichung des eingerammten Monopiles zur Vertikalen ab. Zum Ausgleich für unterschiedliche Abweichungen von der Vertikalen oder auch der Horizontalen können somit verschiedene Distanzringe auf Vorrat hergestellt und entsprechend genutzt werden. (Alfred Schlemenat , ConsysAS-Verbindungstechnologie)