Dezentrale Solarstromspeicher sind ein rasant wachsender Markt. Immer mehr Haushalte entscheiden sich heute, ihren selbst erzeugten Solarstrom in leistungsfähigen Batterien für die Abend- und Nachtstunden zu speichern und sich somit unabhängiger von den großen Energieversorgern zu machen. Im Jahr 2016 wurde bereits fast jede zweite neue PV-Anlage in Privathaushalten mit einem Speichersystem ausgerüstet; in manchen Bundesländern waren es nach ersten Hochrechnungen sogar über 70 Prozent. In Summe führt dieser Trend dazu, dass heute bereits rund 60.000 Speicher mit einer Gesamtkapazität von circa 350 bis 400 Megawattstunden (MWh) in den Verteilnetzen installiert sind.
Die stetig wachsende Anzahl leistungsstarker Batterien in den Haushalten lässt jedoch zwangsläufig auch die Frage nach deren späteren Entsorgungsmöglichkeiten aufkommen: Wie grün sind Heimspeicher tatsächlich und was passiert nach dem Ende ihrer Lebensdauer mit den eingesetzten Batterien?
Zehnjährige Garantie sichert Nachhaltigkeit
Der Aspekt der Nachhaltigkeit von Solarstromspeichern wurde in Deutschland bereits früh von Politik, Forschungsinstituten und Herstellern nachgefragt: Im Rahmen der seit 2013 bestehenden KfW-Förderung wurden verbindliche Mindestgarantiezeiträume festgelegt, die einen ökologisch und ökonomisch nachhaltigen Betrieb der Batteriespeicher sicherstellen. Nach einer anfänglichen Übergangsphase, die eine siebenjährige Garantie vorsah, wird seit Anfang 2016 grundsätzlich eine Mindestgarantiedauer von zehn Jahren eingefordert. Es ist ein starkes Zeichen der Branche, dass sich alle relevanten deutschen Hersteller diesen Nachhaltigkeitszielen verpflichtet haben. Doch irgendwann wird auch die beste Batterie das Ende ihrer technischen Lebensdauer erreichen – wie also können Kunden sicherstellen, dass ihr Heimspeicher sicher abtransportiert und fachgerecht recycelt wird? Hierzu gibt es klare Regeln.
Händler sind zur Rücknahme verpflichtet
In Deutschland ist die Rücknahme, Entsorgung und Verwertung von Batteriespeichern durch das Batteriegesetz festgelegt. Demzufolge kann der Verbraucher PV-Speicher, die das Ende ihrer Lebensdauer erreicht haben, kostenfrei bei einem Vertreiber (zum Beispiel Elektrohandwerker) zurückgeben, wenn dieser PV-Speicherbatterien führt oder geführt hat. Diese Rücknahmepflicht für den Händler gilt unabhängig davon, ob die Batterien bei ihm gekauft wurden oder nicht. Für die nachfolgende Verwertung ist von gesetzlicher Seite eine individuelle Rückgabe einzelner Batteriesysteme an den jeweiligen Hersteller vorgesehen, in dessen Verantwortung auch die letztendliche Verwertung liegt.
Der Regelung folgend müsste daher jeder Händler mit jedem Inverkehrbringer eine Vereinbarung treffen, wie die Batterien des Endnutzers an den jeweiligen Hersteller zurückgegeben werden können. Erschwerend kommt hinzu, dass durch die typen- und markenunabhängige Rücknahmepflicht gegenüber dem Endnutzer auch Produkte von Herstellern beim Händler zurückgegeben werden, zu denen kein Kontakt besteht oder welche gegebenenfalls bereits nicht mehr am Markt aktiv sind.
Gemeinsame Rücknahme sichert reibungslosen Ablauf
Vor diesem Hintergrund haben der Bundesverband Solarwirtschaft (BSW) und der Zentralverband Elektrotechnik- und Elektronikindustrie (ZVEI) als Interessenvertreter der Hersteller, der Zentralverband der Deutschen Elektro- und Informationstechnischen Handwerke als Interessenvertreter der Vertreiber und die GRS Service GmbH bereits frühzeitig den Rahmen eines branchenspezifischen Rücknahmesystems für Industriebatterien zur Verwendung in den oben benannten Anwendungsbereichen beschrieben. Die Vertreiber der Speicher (Händler, Elektrohandwerksbetriebe) sind zwar weiterhin verpflichtet, die ausrangierten Modelle von ihren Kunden unentgeltlich entgegenzunehmen – jedoch entfällt der organisatorische und finanzielle Aufwand, diese individuell den jeweiligen Herstellern zukommen zu lassen, die laut Gesetz für die Entsorgung verantwortlich sind. Durch die Schaffung des Rücknahmesystems ist sichergestellt, dass alle zurückgenommenen Systeme im Auftrag der Herstellergemeinschaft beim Vertreiber abgeholt und einer ordnungsgemäßen Verwertung zugeführt werden.
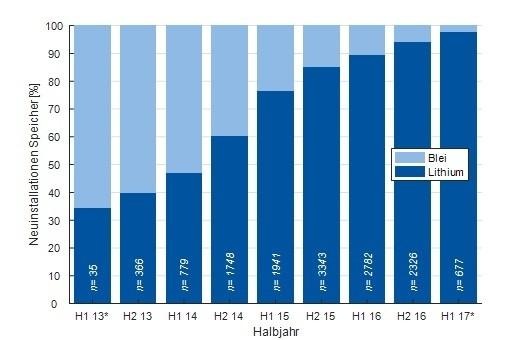
Zuständig hierfür ist die Gemeinsame Rücknahmesystem Servicegesellschaft (GRS) mbH, eine 100-prozentige Tochter der Stiftung GRS Batterien. Sie stellt allen interessierten Vertreibern Sammel- und Transportbehältnisse für die ausrangierten stationären Energiespeicher zur Verfügung. Zudem kümmert sie sich um die Abholung sowie die ordnungsgemäße Behandlung und Verwertung der Produkte. Für die Verkäufer – zum Beispiel Elektrohandwerksbetriebe – entfallen damit aufwendige Sortier- und Weitergabepflichten. Die Hersteller wiederum profitieren, da ihnen die Entsorgung abgenommen wird. Im Rahmen der Branchenlösung, die allen Herstellern zu den gleichen Konditionen zugänglich ist, bietet das System außerdem die Erfüllung der bestehenden Anzeige-, Informations- und Hinweispflichten. Das fachgerecht abtransportierte Heimspeichersystem kann nun in einen Wiederaufbereitungsprozess eingebracht werden. Dieser ist für die verschiedenen am Markt verfügbaren Batterietypen sehr unterschiedlich.
Die Art der Batterie ist entscheidend
Während bis Mitte 2014 noch rund die Hälfte der neu installierten Hausspeicher in Deutschland mit bewährten Bleibatterien ausgestattet wurde, hat sich seitdem die Installationsrate von Hausspeichern mit Lithium-Ionen-Batterien substanziell gesteigert; Anfang 2017 lag diese Quote bereits bei mehr als 95 Prozent. Während die Wiederaufbereitung von Bleibatterien ein seit Langem etablierter Industrieprozess mit umfassenden Erfahrungswerten ist, steht das Recycling von Lithium-Ionen-Batterien heute noch im Fokus von Forschung und Entwicklung, unter anderem im Rahmen des Lithorec-Projekts der TU Braunschweig.
Das Forschungsprojekt Lithorec
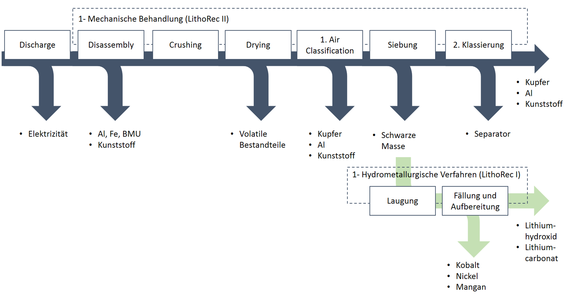
Recyclingprozesse für Lithium-Ionen-Batterien bestehen aus einer Kombination unterschiedlicher Operationen wie Deaktivierung, mechanische Behandlung, hydrometallurgische und/oder pyrometallurgische Prozesse. Während die meisten der bestehenden industriellen Prozesse auf die Rückgewinnung von Materialien mit hohem Marktwert ausgerichtet sind, maximiert ein idealer Recyclingprozess die Menge und Qualität des rückgewonnenen Materials, während die aus dem Prozess resultierenden Umweltauswirkungen minimiert werden. Diese Ziele wurden im Rahmen des Forschungsprojekts Lithorec verfolgt. Die entwickelte Prozesskette ist auf Seite 114 dargestellt. Die Deaktivierung soll die in der Batterie verbleibende elektrochemische Energie reduzieren und damit das Risiko von thermisch-chemischen Reaktionen minimieren. Die vollständige Deaktivierung einer verbrauchten Batterie kann durch Entladung sowie durch die Anwendung von thermischen Behandlungen wie Gefrieren oder Erhitzen bis zum thermischen Durchgehen erreicht werden.
Die mechanische Behandlung folgt mit einer Abfolge von Prozessen, die darauf abzielen, die Batterie in ihre einzelnen Komponenten zu zerlegen. Ein Batteriesystem besteht aus einem Strukturgehäuse und Verbindungskomponenten, einer Batteriemanagementeinheit mit mehreren Leistungselektronikgeräten und Batteriemodulen, die sich aus Batteriezellen zusammensetzen. Die große Anzahl von Komponenten in einem Batteriesystem und die Art, wie diese miteinander verbunden sind, kann aufwendige (manuelle) Demontageschritte erfordern. Automatisierung und moderne Mensch-Roboter-Kooperationen in Produktionsprozessen bieten in dieser Hinsicht die Möglichkeit, Demontagezeiten und auch Kosten zu senken. Sobald die Komponenten voneinander getrennt sind, werden die Batteriemodule in einer inerten Atmosphäre zerkleinert, um das Brandrisiko durch die hochentzündlichen Elektrolytlösungsmittel zu vermeiden. Die zerkleinerten Materialien werden dann in einem Ofen bei Temperaturen zwischen 100 und 140 Grad Celsius getrocknet und die verdampften Lösungsmittel können durch Kondensation gewonnen werden.
Nach dem Trocknungsprozess folgen einige mechanische Trennschritte wie Luftsichten, Zerkleinern und Sieben. Produkte aus diesem Recyclingprozess sind: Aluminium und Kunststoffe aus dem Modulgehäuse, Aluminium aus dem Zellgehäuse, Aluminium und Kupfer aus den Stromsammlern der Zelle und schließlich die sogenannte schwarze Masse, bestehend aus den Beschichtungsmaterialien der Elektroden. Anschließend kann die schwarze Masse in einem hydrometallurgischen Verfahren behandelt werden, in dem Graphit nach einem Laugungsprozess durch Filtration gewonnen wird und die Übergangsmetalle durch pH-Behandlung abgeschieden werden. Die entstandene Li-Lösung wird gereinigt und durch Kristallisation werden festes Lithiumcarbonat oder Lithiumhydroxid gewonnen, aus denen später wieder neue Batterien gebaut werden können. Die kontinuierliche Verbesserung der bestehenden Recyclingprozesse ist ein wichtiger Baustein auf dem Weg zu einer ganzheitlichen, nachhaltigen Versorgung mit erneuerbaren Energien. Doch auch die Hersteller von Speichersystemen sind weiterhin gefragt: Durch gezieltes Design ihrer Produkte hinsichtlich einer optimalen Rezyklierbarkeit können sie ihren ökologischen Fußabdruck von Anfang an auf ein notwendiges Minimum beschränken und somit entlang ihrer gesamten Wertschöpfungskette Ressourcen schonen und unnötige Emissionen vermeiden.
Autoren: Kai-Philipp Kairies, Leiter Netzintegration und Speichersystemanalyse, RWTH Aachen, Tobias Schulze Wettendorf, Leiter Vertrieb und Marketing, GRS, Jan Diekmann, Institut für Partikeltechnik, TU Braunschweig, Felipe Cerdas, Institut für Werkzeugmaschinen und Fertigungstechnik, TU Braunschweig. Dieser Artikel ist bereits in unserem Print-Magazin erschienen. Mehr exklusive Artikel erhalten Sie, wenn Sie jetzt ein kostenloses Probeheft online bestellen.