Zunächst erinnerte Klatt an die Zielmarke: Die Offshore-Branche soll 40 Prozent Kosten einsparen – bis 2020. Eine Studie von Prognos und Fichtner zeigt, welche Bereiche wie viel Prozent zur Kostenreduktion beitragen können. Demnach entfallen auf den Bereich der Fundamente bis zu zehn Prozent der gesamten Einsparungen.
Allerdings sind die Fundamentbauer derzeit kaum in der Lage, dafür große Experimente und Investitionen zu tätigen. Klatt erinnerte daran, dass sich viele Player in den vergangenen Jahren bereits aus dem Markt verabschiedet haben: Hochtief, Siag, Weserwind, Strabag. „Und Bilfinger Marine amp; Offshore Systems GmbH und Bilfinger Mars Offshore stehen zum Verkauf“, fügte er an. Die Herausforderungen – hohe Qualitätsansprüche, geringes Risiko, niedrige Preise – treffen auf eine geschwächte Zulieferindustrie.
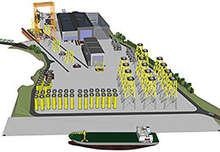
Wenn man über die Fundamentkosten spricht, muss auch von der Art der Fundamente die Rede sein. Während der Konferenz sprachen viele Referenten von ihren Erfahrungen mit XXL-Monopiles. Machbar ist diese Technik auch noch bei einem Pfahldurchmesser von über sechs Metern. Klatt gehörte zu denjenigen, die Monopiles nur bis zu einer Wassertiefe von 40 Metern für sinnvoll halten. Darüber hinaus sind Jackets eine mögliche Form. Ab 60 Metern werden künftig möglicherweise Schwimmfundamente das Mittel der Wahl sein.
Was die großen Aufgaben anbelangt, die auf die Branche nun warten, fragte Klatt: „Was haben wir bei Bilfinger Offshore getan, um die Herausforderungen bezüglich der Kostensenkung anzunehmen? Wir haben eine Serienfertigung auf der grünen Wiese aufgebaut. Dort können wir mindestens 50 Jackets pro Jahr fertigen.“ Die Fabrik, die Bilfinger zusammen mit Mars aufgebaut hat, befindet sich im Hafenbereich der polnischen Stadt Stettin. Die Produktion läuft seit Juli, im Dezember wird der Portalkran noch ergänzt und dann ist alles komplett. Zusätzlich zu den Jackets werden dort pro Jahr 80 Komponentensets und bis zu 80 Piles gefertigt. Zudem gibt es die Möglichkeit, die Fabrik zu vergrößern.
Jackets sind wegen ihrer aufwändigen Gitterstruktur eine Herausforderung für Schweißer. Die neue Produktion ist nun mit Schweißrobotern ausgestattet. In einem Filmchen demonstriert Klatt, wie ein Roboter von außen die Schweißspalt scannt und die Mikrogeometrie speichert, um dann hochpräzise die Wurzelnaht zu schweißen. „Menschen können das nicht“, betont Klatt. Auf diese Weise lassen sich ein bis anderthalb Jackets pro Woche fertigen.
Kostensenkungspotenzial sieht Klatt an verschiedenen Stellen. "Aufgrund des Einsatzes von Standardrohren sinkt der Preis für die Stahllieferung um bis zu 30%", erklärte der Bilfinger-Manager. Wichtig sei auch die Industrieproduktion: 65 bis 80 Prozent der Materialien, die eingesetzt werden, sind Standardrohre. Schon heute könne Bilfinger Jackets mit 40 m Wassertiefe bei 80 mal 6-MW-Turbinen günstiger herstellen. "In diesem einen Fall haben wir herausgefunden, dass das Jacket die günstigste Variante darstellt. Solche Betrachtungen sind immer projektspezifisch zu machen", so Klatt.
Die Fabrik hat bereits einen ersten Auftrag abzuarbeiten. Dong hat 91 Transition Pieces für den Windpark Race Bank bestellt. (Nicole Weinhold)