Knapp drei bis vier Stunden müssen Kletterer inzwischen gehen, um die schon 80 Meter langen Rotorblätter der jüngsten Turbinenklasse für Windparks an Land am Seil schwebend beidseitig abzuschreiten. Während sie sich von der Maschinenhausgondel am abwärts gestellten Rotorblatt abseilen, gucken sie Schäden aus und legen den Reparaturbedarf fest. Angesichts der enormen Blattdimensionen mögen sie an die 1988 von der Deutschen Bahn abgeschafften Streckengeher zum Prüfen der Gleise erinnern. Doch noch sind Seilkletterer dank ihrer Gründlichkeit für die Branche wichtig. Allerdings übernimmt die Automatisierung von Schadensinspektion und Zustandsüberwachung in vielen Windparks nun eine Führungsrolle. Kamerabewehrte Flugdrohnen, Reparaturroboter, Laserkameras und Rotorblattsensoren gewinnen dank innovativer Anbieter bei Investoren, Windturbinen-, Finanz- und Betriebsführungsunternehmen an Akzeptanz.
So wie On-Site-Service aus Kleve (siehe Interview auf Seite 28). Seit 2016 entwickelten Dirk Marche und Markus Terheiden ihre Inspektionstechnik einer handgesteuerten einfachen Consumer-Flugdrohne. Drohnenpilot Marche lässt sie mit einem Abstand von acht Metern die Rotorblätter abfliegen und Kameramann Terheiden erstellt Bilder mit einem Volumen von 20 Megapixel. Kleine Haarrisse von mehreren Millimetern Länge werden so sichtbar. Bei günstigem Wetter kann das Duo mit einer thermografischen Wärmebildkamera auch verdächtige Stellen leicht unterhalb der Blattoberfläche aufzeichnen. Sie professionalisierten ihre Flugroutine so, dass sie einen Rotorstern mit 160 Meter Durchmesser binnen maximal einer Stunde abfliegen können, wie Terheiden erklärt. Bei einer von vielleicht zehn Windenergieanlagen müssen die Kletterer wegen nicht eindeutiger Aufnahmen verdächtige Zonen am realen Blatt erneut in Augenschein nehmen, sagt Marche. Im Vergleich zu den Seilkletterern spürt On-Site-Service mit einer zeitlichen Differenz von acht bis zwölf Stunden weniger auf, wo Schäden am Blatt zu erkennen sind. Dadurch könne On-Site-Service schon sagen, an welchen Stellen Seilkletterer mit Glasfaserkunststoffflicken zur Reparatur aufsteigen sollten.
Seit Mitte 2020 gehen die Aufträge massenweise ein, so schildern es Terheiden und Marche – „bei Inspektionen von Woche für Woche in mehreren Windparks“. Auch künstliche Intelligenz bringt das Duo vom Niederrhein auf Kundenwunsch zum Einsatz. Hierfür arbeiten sie mit dem Drohnenfluganbieter Aero Enterprise zusammen. Sie nutzen das Computerprogramm der Österreicher, mit dem sich neue Aufnahmen mit Aufnahmen vom Vorjahr abgleichen lassen und kleinste Schäden durch eine KI vorab erkannt werden. Das Programm errechnet daraus Prognosen zur Weiterentwicklung kleinerer Schäden: Wann eine kritische Schwelle überschritten ist und die Reparatur erforderlich wird.
Eine Vielzahl von Unternehmen bietet so Dienste zur Beschleunigung und Kostensenkung der Rotorblattinspektionen an. Es ist ein für Kunden vorteilhafter Wettbewerb mit einem breiten, technologisch reifen Angebot. Ob Aero Enterprise mit intelligenter Datenverarbeitung und einer Kombination aus einer auf 62 Megapixel hochauflösenden Drohnenlinse und einer Tiefenschäden aufspürenden Infrarotkamera, ob Sulzer und Schmid mit zusätzlicher Auswertung der Daten durch geschulte Blattexperten, ob Supairvision mit einer manuell gesteuerten Drohnen-Kamera-Fahrt im Abstand von nur drei Metern zum Blatt und 45 Megapixel Auflösung oder Nawrocki Alpin, das eine am Boden aufgeständerte Kamera einsetzt. Diese dreht sich der Bewegung des Rotors folgend um die eigene Achse und dokumentiert im laufenden Turbinenbetrieb den Blattoberflächenzustand. Auch die Wartungsunternehmen Enertrag Windstrom und Robur Wind bieten einen Drohneneinsatz mit an – in Partnerschaft mit Sulzer und Schmid aus der Schweiz sowie mit Aero Enterprise. Robur Wind nutzt zudem Kamera-Roboter im Blattinnern. Manche Anbieter schicken eigene Drohnenpiloten. Andere übergeben in Lizenz die Steuerungs- und Auswertungs-Software an die Kunden und schulen diese in der Bedienung autonom fliegender Multikopter.
TOPseven aus dem bayerischen Starnberg übergibt den Kunden die eigens entwickelte Software für die Industriedrohne DJI M300, die sich die Kunden kaufen (siehe Interview auf Seite 29). Von TOPseven geschulte Kunden können anschließend die Inspektion an Rotorblättern und Turm eigenständig durchführen – die Drohne fliegt dabei autonom. Eine künstliche Intelligenz (KI) unterstützt bei der Analyse der Daten und erstellt automatisiert den standardisierten Prüfbericht.
TOPseven-Alleinstellungsmerkmal ist aber die berührungslose Blitzschutzmessung per Drohne. Als erstes Unternehmen bietet es, validiert und verifiziert von TÜV Süd, dieses alternative Messverfahren an. „Laut Richtlinie zur Prüfung der Blitzschutzanlage an Windenergieanlagen des Bundesverband Windenergie von März 2021 dürfen auch alternative Prüfmethoden eingesetzt werden, wenn diese von einer unabhängigen Stelle erfolgreich validiert und verifiziert wurden“, informiert das Unternehmen. Dies ist im Juli 2021 durch den TÜV Süd erfolgt. Für die Messung erzeugt ein Signalgenerator an der Blattwurzel ein elektrisches Feld am Blitzableiter entlang des Rotorblattes. Eine mit einem Sensor zur Feldmessung ausgestattete Drohne fliegt zur Rotorblattspitze und misst, ob und wie stark ein Signal ankommt. Anschließend fliegt sie das Rotorblatt in Richtung Blattwurzel ab. Fehlt das Signal an der Blattspitze, misst die Drohne, wo es einsetzt: An dieser Stelle liegt folglich der für die Feldunterbrechung verantwortliche Blitzableiterschaden. Die Drohne fliegt das Blatt immer ab, falls das Signal aufgrund einer Korrosion beispielsweise abgeschwächt ankommt. Dann identifiziert sie, wo die Signalschwächung und folglich der Rostschaden sein muss.
Drohnen sind nicht das einzige Instrument, das die Überwachung der Funktionstüchtigkeit des Rotors automatisiert. Windcomp aus Berlin stellt ein Doppellaser-Messsystem am Boden auf ein Stativ und identifiziert kleine Abweichungen im Stellwinkel der Rotorblätter (siehe Interview auf Seite 30). Es analysiert, ob diese noch tolerable 0,3 oder wenigstens 0,6 Grad betragen, oder mit einem Grad gegen Betriebsauflagen verstoßen. Die Messung im laufenden Betrieb stellt auch Abweichungen im Twist fest – der aerodynamischen Verbiegung des Blattprofils um die eigene Achse sowie der Vorbiegung in der Länge der zunehmend massereduzierter, elastisch ausgelegten Komponente. Zudem misst Windcomp die Turmschwingungen oder die 120-Grad-Blattspreizungen im Rotorkreis und leitet aus Messdaten auch Masseunwuchten ab.
Die nicht seltenen Blattfehlstellungen verursachen ab einem Grad Winkelabweichung schon Ertragsverluste von zwei Prozent und mehr. Windcomp-Geschäftsführer Dietrich Mayer setzt sein System seit 2010 ein. Er sieht die Lasertechnologie im Wettbewerb zu konventioneller Kameratechnik der traditionellen Rotorblatt-Unwuchtmessung dank immer besserer Sensorik, Laser und Algorithmen im Vorteil. Im Verbund mit Forschungseinrichtungen arbeitet er an einer KI, die auch Gewichtsunterschiede automatisiert beziffert. Mit der Rotorblattlänge wächst geämß Mayers Beobachtung der Bedarf. Denn die unter ihrem hohen Eigengewicht in vertikaler Position sich sehr stark durchbiegenden Komponenten erlauben seiner Meinung nach keine geeignete Messung oder abweichungsfreie Produktion im Werk mehr.
Die Besteller automatisierter Rotorinspektionen sind häufig Betriebsführungsunternehmen, Windturbinenhersteller oder Wartungsdienstleister. „Zukünftig werden Inspektionen an Rotorblättern mittels Drohnen die Seilzugangstechnik ersetzen“, heißt es bei einem solchen Wartungsdienst. Vielleicht wird dies in nicht so ferner Zukunft schon einsetzen: Schon bei „Nabenhöhen ab 100 Metern und Rotordurchmessern ab 77 Meter“ sei „der Einsatz aus Sicht des Arbeitsschutzes und der Wirtschaftlichkeit zu bevorzugen“.
Windturbinenbauer Siemens Gamesa (SGRE) will jedenfalls 2022 von bodenbasierten Kameras auf Drohnen umstellen. Den vom Siemens-Gamesa-Service betreuten Windparkbetreibern verspricht das deutsch-dänisch-spanische Unternehmen, mittels Drohnen „in weniger als einer halben Stunde hunderte von hochauflösenden Fotos“ zugänglich zu machen, die mit „künstlicher Intelligenz in Sekundenschnelle zu einem 3-D-Bild des Rotorblattes zusammengefügt“ und „mithilfe eines Algorithmus analysiert und in unsere Vorhersagemodelle eingespeist“ werden.
Denn dies soll die neue Zielrichtung im Service sein: Mit intelligenten Vorhersagemodellen die Zeiten und Kosten der Wartung reduzieren. Durch maschinelles Lernen, fortschrittliche Simulationen und Analysen, risikobasierte Inspektionen, präventive Upgrades und Echtzeit-Überwachung soll der Instandhaltungsdienst die Anlage proaktiver fit halten und Schäden vorbeugen.
Wie sehr sich der Service im Detail verändert, wird SGRE also vorführen. Als erstes sollen die Kunden aber mehr Nachvollziehbarkeit gewinnen. Eine Visual Based Asset Integrity (VBAI) genannte Plattform gewährleiste den Kunden den Zugriff auf alle Drohneninspektionsbilder und Metadaten, lasse sie in Inspektionsbilder hineinzoomen oder einen zusammengefassten Überblick studieren, erklärt das Unternehmen.
Auch im Rotorblatt-Monitoring nimmt die Sicherheit durch Automatisierung zu. So meldete nun Wölfel Engineering aus Hochberg bei Würzburg eine Kombination der eigenen Blattstrukturüberwachungstechnik mit dem Lastmonitoring von Phoenix Contact.
Wölfel baut dafür sein auf Beschleunigungssensoren fußendes System Structural Health Monitoring Blade (SHM Blade) über ein Software-Modul in das Lastüberwachungssystem des Partners ein, das Blade-Intelligence-System. Durch ein lernendes Programm soll es kleinste Veränderungen in der Blattstruktur frühzeitig identifizieren – und in Kombination mit der Lastmessung, der Blitz- und Eiserkennung der Phoenix-Contact-Technologie „einen erheblichen Mehrwert für Windparkbetreiber“ schaffen. Mehr Erträge dank mehr Last- und Schadenvermeidung lautet diese Devise.
Um die Rotorbetriebskosten zu reduzieren, lässt sich auch bedeutend vorher automatisieren: In der Blattproduktion hat das hessische Spezialunternehmen Tartler vor gut eineinhalb Jahren ein Schlauchsystem zur Vakuuminfusion eingeführt. Tartlers Misch- und Zuleitungstechnik füllt die als Bindemittel eingesetzten Kunstharze in die mit Glasfasermatten ausgelegten Rotorblattbauschalen, die den Harz unter Vakuumunterdruck einsaugen, erwärmen und aushärten.
Tartlers neues System kommt anders als herkömmliche Systeme ohne Eimer oder Säcke für den Kunstharz aus. Vielmehr findet bereits das Mischen im Zuleitungsschlauch unter Vakuum statt, woraus der Harz direkt in das Vakuum der Blattform weiter fließt. „Lufteinschlüsse im Harz, die zu Schäden führen können, gibt es da nicht mehr“, sagt Geschäftsführer Udo Tartler. Nacharbeiten zur Beseitigung von Blasen beträfen statt 93 Prozent nur noch 2 Prozent der Rotorblätter.
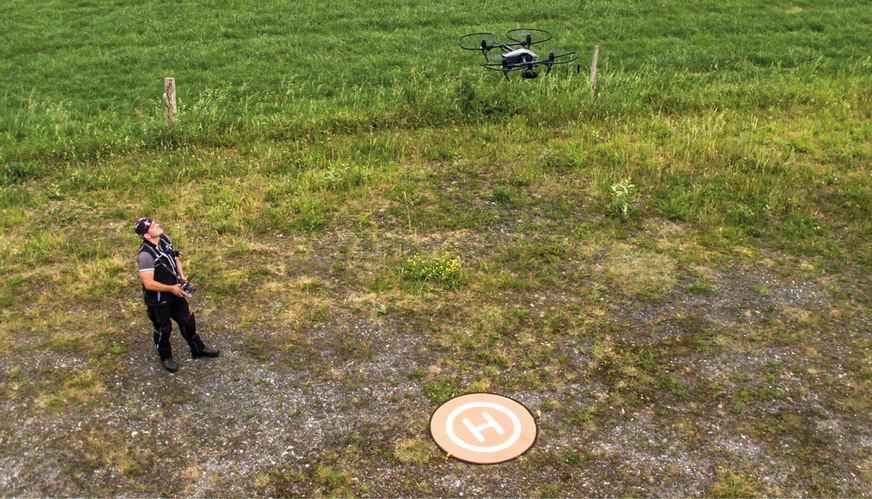
Foto: 0n-Site-Service
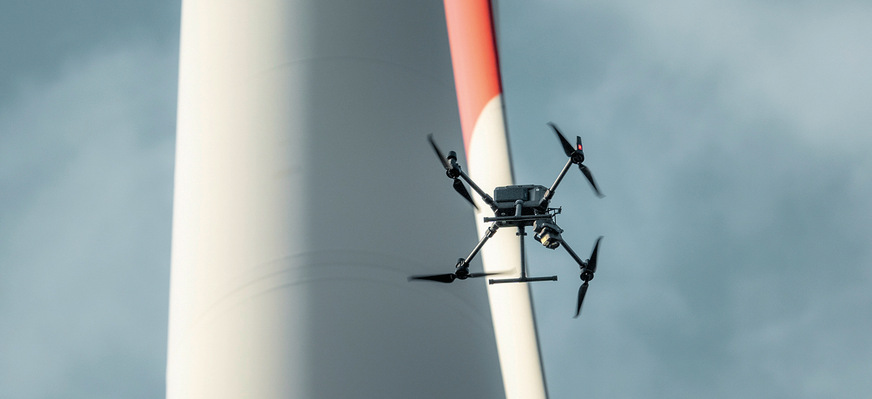
Foto: TOPseven
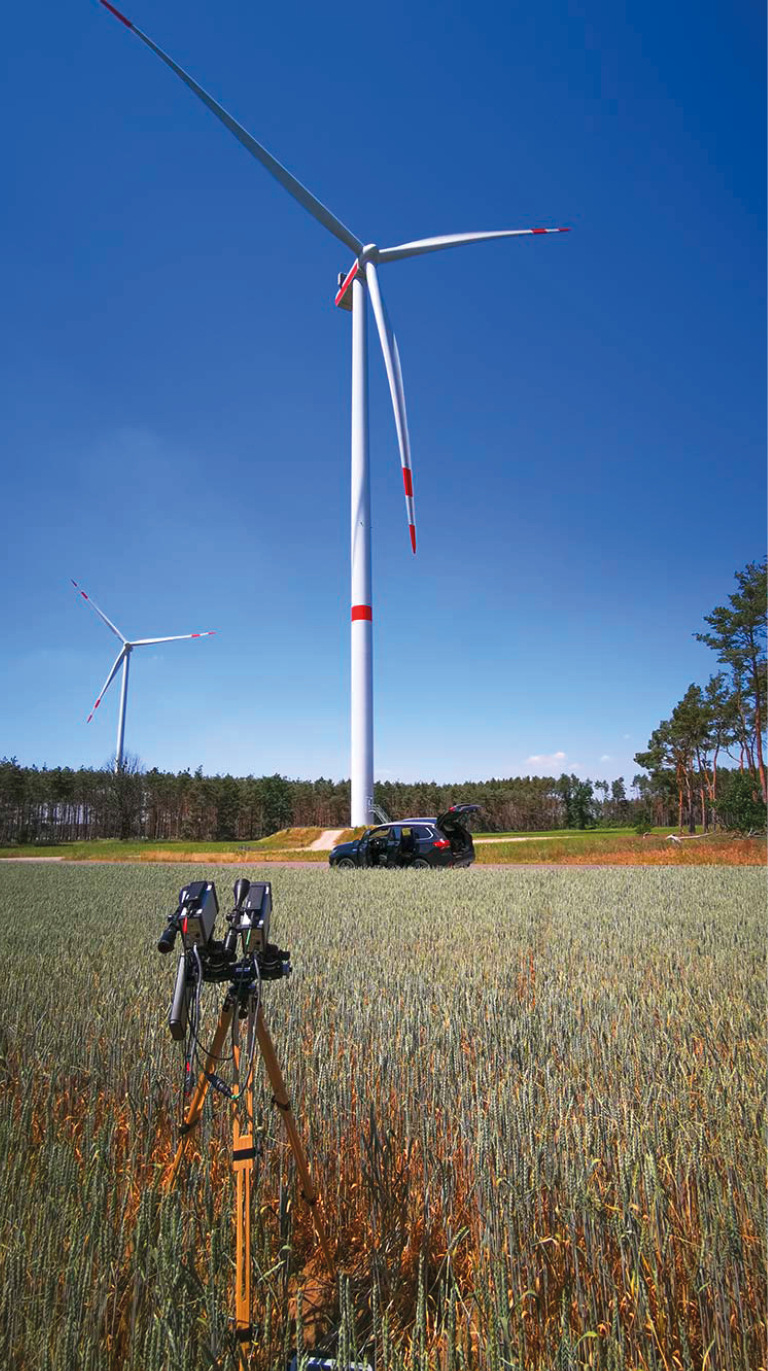
Foto: windcomp
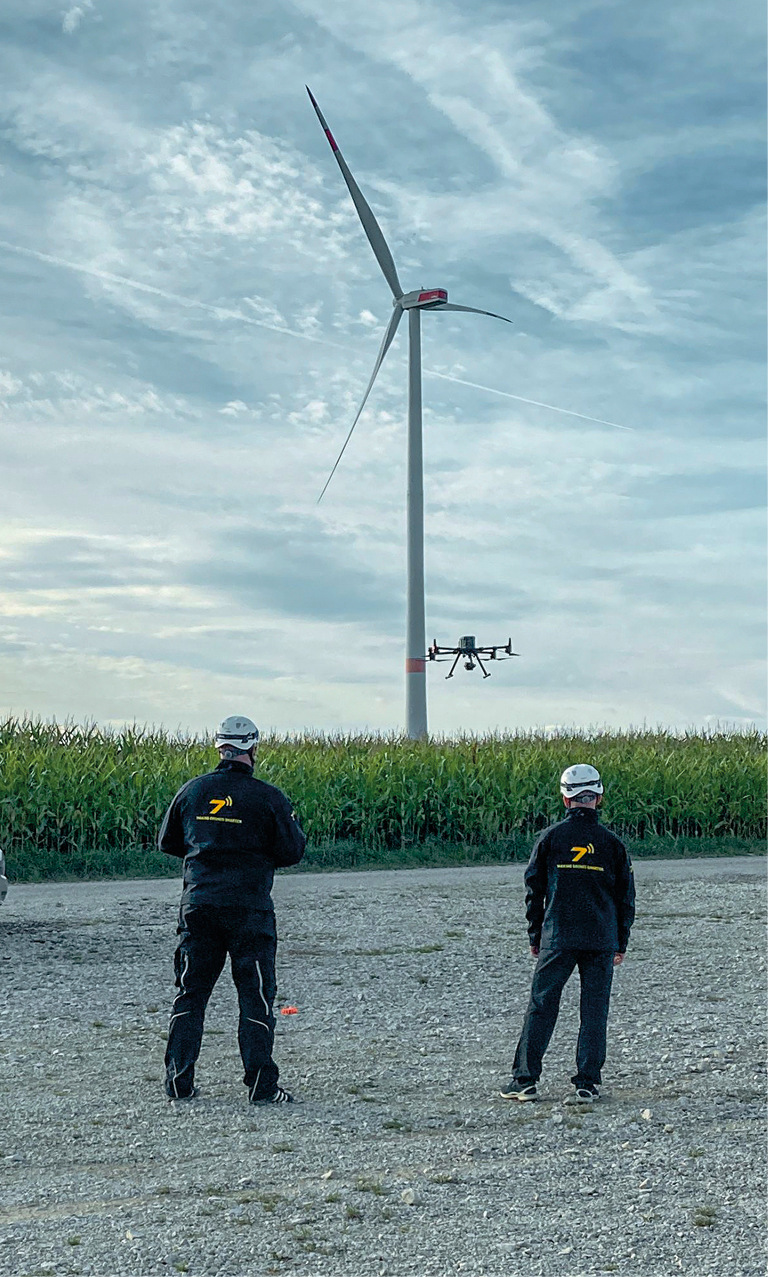
Foto: TOPseven
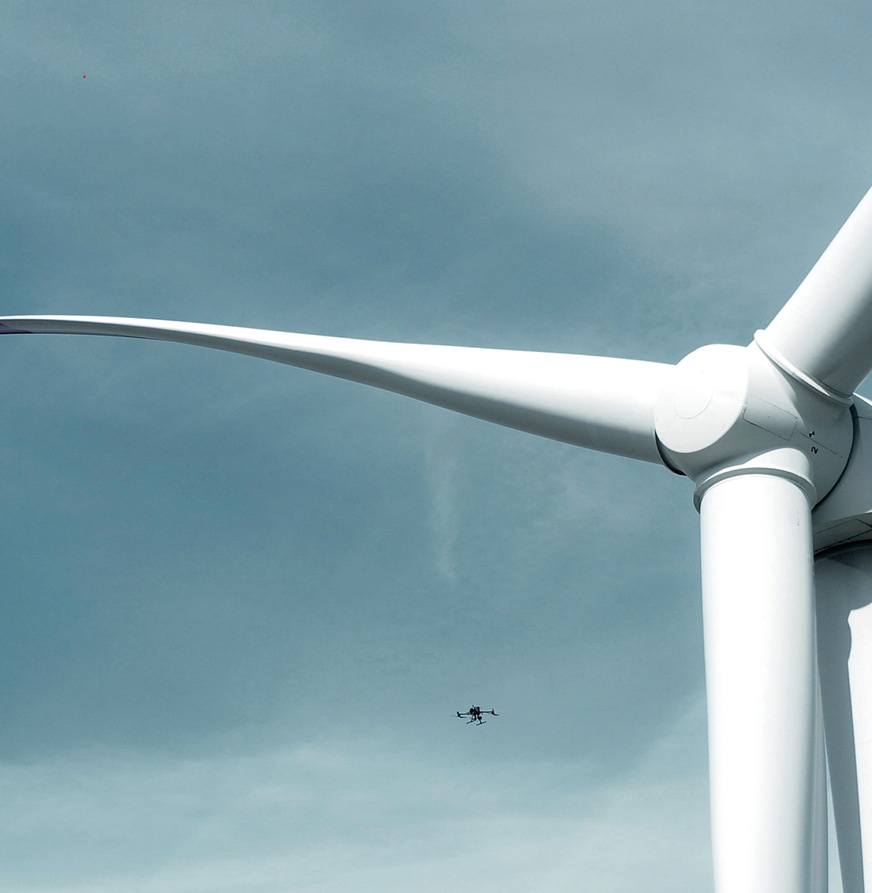
Foto: TOPseven
On-Site-Service
Tel. 02821/7415864
Siemens-Gamesa
Tartler
Tel. 06061/9672-0
Topseven
Tel. 08151/95966-0
Windcomp
Tel. 030/319855475
Wölfel
Tel. 0931/49708-0