Verkeilte Turmsegmente erhöhen möglicherweise die Automatisierung im Aufbau des für die wachsenden Nabenhöhen entscheidenden Bauwerks. Vor allem könnten sie die Kapazität des Turms für höhere Lasten und Biegemomente wesentlich stärken. Das anfangs von Forschern der Universität TU Delft begleitete Entwicklungsprojekt Wedge Connection – auf Deutsch: eine Keilverbindung – kam erstmals 2021 in einer 14 Megawatt (MW) leistenden Windturbine in Norddänemark zum Einsatz.
Nun hat sich Anfang Juli ein Konsortium aus zwölf führenden Meereswindkraft-Akteuren und dem für die Innovation verantwortlichen niederländischen Unternehmen C1 Connections vorgestellt, das den kommerziellen Einsatz der verkeilten Türme erreichen soll.
Die Entwicklung zielt zunächst auf ein Lastenproblem der Türme, das eine kritische Schwelle zu erreichen droht. Zugleich soll Wedge Connection die Belastung der Montagearbeiter beim Aufbau der Türme reduzieren, wo diese heute sehr schwere Bolzen einsetzen und ebenso gewichtige Werkzeuge zum Anziehen der Schrauben nutzen müssen. Bei Windturbinen von mehr als 15 Megawatt (MW) Nennleistung und mehr als 200 Meter Rotordurchmesser, die es vorerst nur auf Offshore-Stellflächen geben wird, bei künftig höheren Türmen nicht mehr nur an Land sondern auch auf See, erreichten Kipp- und Biegemomente am Turmansatz und in unteren Turmbereichen inzwischen Lastenwerte in Giganewtonmeterdimension, sagt Jasper Winkes, der Geschäftsführer der Niederländer.
Turmdesigner müssten künftig entweder den nach dem Turmquerschnittprofil benannten L-Flansch mit im Turm gelegenem Bolzenkreis durch den aufwändigeren T-Flansch mit einem zusätzlichen äußeren Bolzenkreis ablösen, so denkt Jaspers laut nach. Das wäre nach Einschätzung des niederländischen Entwicklers aber für die meisten Meeresstandorte keine Option. Oder sie müssten wie an Land große Türme mit Betonsockeln von bis zu acht Metern Durchmesser versehen, die sich nach oben verjüngen und oben den Stahlturm tragen – aufgrund des Kostendrucks auf See wäre auch dies sicherlich keine Option.
Steckschnittstelle ersetzt Flansche
Die von Winkes geführten Entwickler ersetzen die Flanschverbindung durch eine neue Steckschnittstelle. Wo sich vorher die Flansche mit ihren Bohrungen für die Bolzen aneinanderfügen mussten wie eben ein aufrechtes und ein nach unten gespiegeltes L, steckt jetzt um im Bild zu bleiben ein angedicktes kleines l als Profil des unteren Turmsegments in einem nach unten zeigenden U-Profil des oberen Stahlzylinders. Das l-Profil ist durchgängig im gesamten Radius mit ovalen Öffnungen gespickt. Die Innenseite des U-Profils ist ebenso mit ovalen Öffnungen versehen, die deckungsgleich zu den Bohrungen des l-Profils sind. An der U-Innenseite angebrachte waagerechte Ladevorrichtungen tragen die innovativen Keile. Stecken die Turmsegmente ineinander, schieben Arbeiter die Keile ein und drehen mit dem Schrauber eine Mutter zu, die um eine aus dem Keil ragende Gewindestange steckt. Dies zieht die Gewindestange heraus, deren spezielle Geometrie im Innern des Keils die Spreizung auslöst.
Hierbei drückt der Keil das obere Turmsegment nach unten und presst zugleich gegen den oberen Lochrand des unteren Turmsegments – und entfaltet somit die hohe Festigkeit einer Keilverbindung durch deren Kombination aus Reibung, Zug- und Druckkräften.
Kleinere Schrauben genügen
Zugleich genügen kleinere Schrauben: „Bolzen der Größe M42 statt M72 bis M80“, sagt Winkes. „Wir sparen 50 Prozent Gewicht und können ein Turmsegment in der halben Zeit montieren.“ Schraub- beziehungsweise Installationswerkzeuge mit unter 10 bis nur wenig mehr als 15 Kilogramm Gewicht genügen. Auch das Zusammenfügen der Turmsegmente soll ohne Arbeiter gelingen, die bisher beim Kranhub eines Turmsegments das Zusammenkommen der Flanschlöcher von Hand steuern mussten. Trichterförmige Senkführungen an zwei Stellen des unteren Segments und Führungsstahlstifte im oberen Segment lassen die Turmabschnitte exakt in die richtige Position zueinander rutschen.
Angeblich bewies sich die Keilverbindung in der Pilot-Windenergieanlage in Dänemark als stabil. „Wir sind jetzt technisch bereit. Unsere Partnerunternehmen machen nun den nächsten Schritt“, sagt Winkes. (tw)
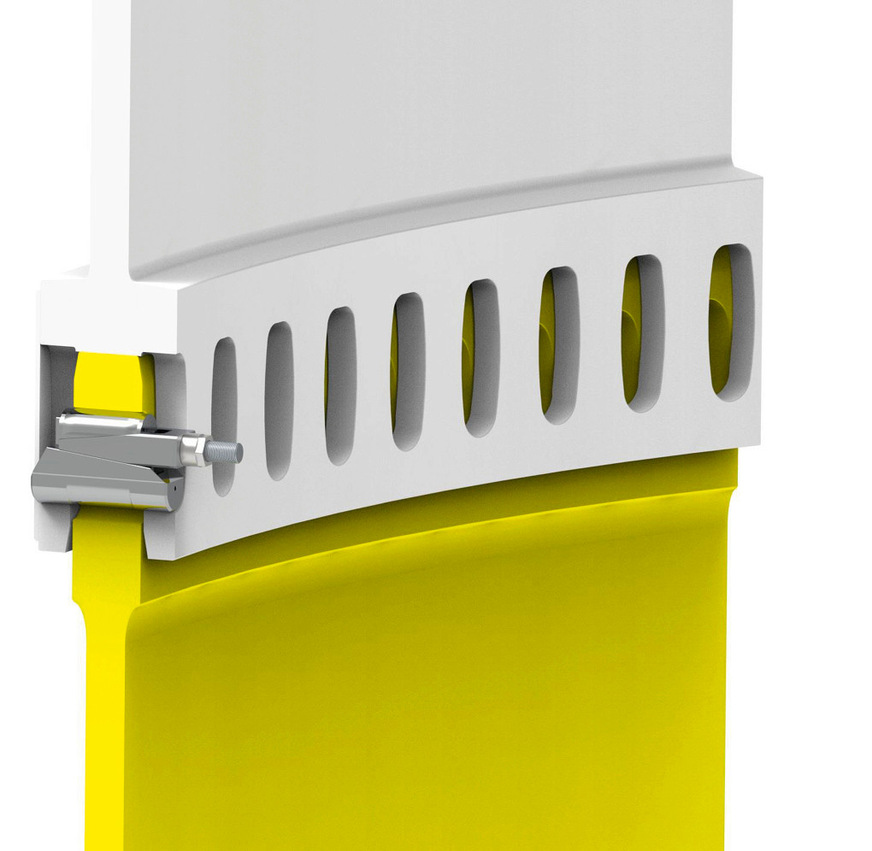
Bild: C1 Connections